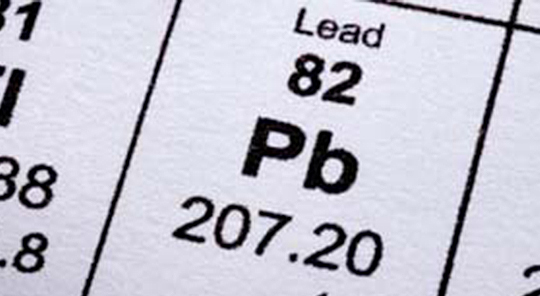
Contents
Overview
Lead overexposure is one of the most common over exposures found in industry and is a leading cause of workplace illness. The reduction of lead exposure is a high strategic priority. OSHA five year strategic plan sets a performance goal of a 15% reduction in the average severity of lead exposure or employee blood lead levels in selected industries and workplaces.
Process, Control & Technical Information:
The following information that describes facility specific information concerning processes and controls are maintained as an addendum to this written program:
a. Description of each operation in which lead is emitted; e.g. machinery used, material processed, controls in place, crew size, employee job responsibilities, operating procedures and maintenance practices.
b. Description of the specific means used to achieve compliance, including engineering plans and studies used to determine methods selected for controlling exposure to lead.
c. Report of the technology considered in meeting the permissible exposure limit;
d. Air monitoring data which documents the source of lead emissions;
e. A detailed schedule for implementation of this program, including documentation such as copies of purchase orders for equipment, construction contracts, etc.
f. Records of Employee Training and Notifications
g. Specific work practice program and controls for each operation involving lead exposure
h. Administrative control schedule
i. All other relevant information
Hazards:
Pure lead (Pb) is a heavy metal at room temperature and pressure and is a basic chemical element. It can combine with various other substances to form numerous lead compounds. The Permissible Exposure Limit (PEL) set by OSHA is 50 micro grams of lead per cubic meter of air (50 ug/m(3)), averaged over an 8-hour workday.Lead can be absorbed by inhalation (breathing) and ingestion (eating). Lead is not absorbed through your skin. When lead is scattered in the air as a dust, fume or mist it can be inhaled and absorbed through the lungs and upper respiratory tract. Lead can also be absorbed through the digestive system if swallowed. Handling food, cigarettes, chewing tobacco, or make-up which have lead contamination or handling them with hands contaminated with lead, will contribute to ingestion.A significant portion of inhaled or ingested lead goes into the blood stream. Once in the blood stream, lead is circulated throughout the body and stored in various organs and body tissues. Some of this lead is quickly filtered out of the body and excreted, but some remains in the blood and other tissues. As exposure to lead continues, the amount stored in the body will increase. Lead stored in body tissues can cause irreversible damage, first to individual cells, then to organs and whole body systems.
Short-term (acute) effects of overexposure to lead:
Lead is a potent, systemic poison. Taken in large enough doses, lead can kill in a matter of days. A condition affecting the brain called acute encephalitic may arise which develops quickly to seizures, coma, and death from cardio respiratory arrest. There is no sharp dividing line between rapidly developing acute effects of lead, and chronic effects which take longer to acquire. Lead adversely affects numerous body systems, and causes forms of health impairment and disease which arise after periods of exposure as short as days or as long as several years.
Long-term (chronic) effective of overexposure to lead:
Chronic overexposure to lead may result in severe damage to blood-forming, nervous, urinary and reproductive systems. Some common symptoms of chronic overexposure include loss of appetite, metallic taste in the mouth, anxiety, constipation, nausea, pallor, excessive tiredness, weakness, insomnia, headache, nervous irritability, muscle and joint pain or soreness, fine tremors, numbness, dizziness, hyperactivity and colic. In lead colic there may be severe abdominal pain.
Monitoring:
Initial determination.
The company has made an initial determination of lead work areas and exposure levels and will conduct subsequent “initial determinations” in the event of changes to hazard control methods or operational processes that affect employee or environmental exposure. Initial determinations are conducted to determine if any employee may be exposed to lead at or above the action level of 30 micro grams per cubic meter of air (30 ug/m(3)) averaged over an 8-hour period.
Where a determination is made that no employee is exposed to airborne concentrations of lead at or above the action level, the company shall maintain a written record. The record shall include quantitative sampling data, date of determination, location within the work site, and the name and social security number of each employee monitored.
Monitoring requirements:
- Monitoring and analysis methods shall have an accuracy (to a confidence level of 95%) of not less than plus or minus 20 percent for airborne concentrations of lead equal to or greater than 30 ug/m(3).
- Where a determination shows the possibility of any employee exposure at or above the action level, the company shall conduct monitoring which is representative of the exposure for each employee in the workplace or process area who is exposed to lead.
- For the purposes of monitoring requirements, employee exposure is that exposure which would occur if the employee were not using a respirator.
- Monitoring and sample collection shall cover full shift (for at least 7 continuous hours) personal samples including at least one sample for each shift for each job classification in each work area.
- Full shift personal samples must be representative of the monitored employee’s regular, daily exposure to lead.
Monitoring Frequency:
At or Above Action Level and Below PEL:
Every 6 months ff the initial determination or subsequent monitoring reveals employee exposure to be at or above the action level but below the permissible exposure limit. This monitoring (6 month frequency) will continue until at least two consecutive measurements, taken at least 7 days apart, are below the action level.
Above PEL:
If the initial monitoring reveals that employee exposure is above the permissible exposure limit the company will repeat monitoring quarterly. Quarterly monitoring will continue until at least two consecutive measurements, taken at least 7 days apart, are below the PEL but at or above the action level.
Additional monitoring:
Whenever there has been a production, process, control or personnel change which may result in new or additional exposure to lead, or whenever any other reason to suspect a change which may result in new or additional exposures to lead, additional monitoring will be conducted.
Employee Notification of Monitoring Results:
Within 5 working days after the receipt of monitoring results, each employee will be notified in writing of the results which represent that employee’s exposure.Whenever the results indicate that the representative employee exposure, without regard to respirators, exceeds the permissible exposure limit, the the written notice will include a statement that the permissible exposure limit was exceeded and a description of the corrective action taken or to be taken to reduce exposure to or below the permissible exposure limit.
Observation of monitoring:
The company provides affected employees or their designated representatives an opportunity to observe any monitoring of employee exposure to lead.
Health Effects
Workers today are still being exposed to lead that result in adverse health effects. Recent studies have provided evidence that lead can cause health effects at blood lead levels lower than those established by OSHA’s 1978 Lead standard.
Epidemiological and experimental studies indicate that chronic exposure resulting in blood lead levels (BLL) as low as 10 µg/dL in adults are associated with impaired kidney function, high blood pressure, nervous system and behavioral effects, cognitive dysfunction later in life, and subtle cognitive effects attributed to prenatal exposure. Pregnant women need to be especially concerned with reducing BLL since this can have serious impact on the developing fetus.
Chronic exposures leading to BLLs above 20 µg/dL can cause sub clinical effects on cognitive functions as well as adverse effects on sperm/semen quality and delayed conception. BLLs between 20 to 40 µg/dL are associated with effects such as cognitive aging as well as deficits in vasomotor dexterity, lower reaction times and attention deficit. At BBLs above 40 µg/dL, workers begin to experience symptoms such as headache, fatigue, sleep disturbance, joint pain, anorexia, and constipation.
While much less common today, workers can be exposed to high lead levels resulting in BLL over 60 µg/dL. Health effects at these very high BLLs can range from acute effects such as convulsions, coma, and in some cases, death, to more chronic conditions such as anemia, peripheral neuropathy, interstitial kidney fibrosis, and severe abdominal cramping.
Engineering Controls:
Where any employee is exposed to lead above the permissible exposure limit for more than 30 days per year, the company will implement feasible engineering and work practice controls (including administrative controls) to reduce and maintain employee exposure to lead. Wherever the engineering and work practice controls which can be instituted are not sufficient to reduce employee exposure to or below the permissible exposure limit, the company will still use them to reduce exposures to the lowest feasible level and shall supplement them by the use of respiratory protection. Where any employee is exposed to lead above the permissible exposure limit, but for 30 days or less per year, the company will implement engineering controls to reduce exposures to 200 ug/m(3), but thereafter may implement any combination of engineering, work practice (including administrative controls), and respiratory controls to reduce and maintain employee exposure to lead to or below 50 ug/m(3).
Mechanical ventilation: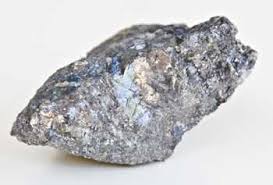
When ventilation is used to control exposure, measurements which demonstrate the effectiveness of the system in controlling exposure, such as capture velocity, duct velocity, or static pressure shall be made at least every 3 months. Measurements of the system’s effectiveness in controlling exposure shall be made within 5 days of any change in production, process, or control which might result in a change in employee exposure to lead.
Recirculation of air. If air from exhaust ventilation is recirculated into the workplace, the system must include:
- a high efficiency filter with reliable back-up filter; and
- controls to monitor the concentration of lead in the return air and to bypass the re circulation system automatically if it fails are installed, operating, and maintained.
Administrative Controls:
If administrative controls are used as a means of reducing employees TWA exposure to lead, the company shall establish and implement a job rotation schedule which includes:
- Name or identification number of each affected employee ,
- Duration and exposure levels at each job or work station where each affected employee is located.
- Other information which may be useful in assessing the reliability of administrative controls to reduce exposure to lead Administrative control information and records will be maintained as an addendum to this written program.
Controlling Exposure:
Workers are primarily exposed to lead by breathing in particles containing lead. Lead compounds can also get on the skin, contaminate clothing or food, and be ingested . The most effective way to prevent exposure to a hazardous material such as lead is through elimination or substitution with viable, less toxic alternatives. The hierarchy of controls describes the order that should be followed when choosing among exposure-control options for a hazardous substance. Generally, elimination or substitution is the preferred choice (most protective) at the top of the hierarchy, followed byengineering controls, administrative controls, work-practice controls, and, finally, personal protective equipment (PPE). Engineering controls include isolating the exposure source or using other engineering methods, such as local exhaust ventilation, to minimize exposure to lead. Administrative controls usually involve logistic or workforce actions such as limiting the amount of time a worker performs work involving potential exposure to lead. When exposure to lead hazards cannot be engineered completely out of normal operations or maintenance work, and when safe work practices and other forms of administrative controls cannot provide sufficient additional protection, a supplementary method of control is the use of protective clothing or equipment. This is collectively called personal protective equipment, or PPE. PPE may also be appropriate for controlling hazards while engineering and work practice controls are being installed. PPE includes wearing the proper respiratory protection and clothing. Good housekeeping practices to prevent surface contamination and hygiene facilities and practice to protect workers from ingesting and taking home lead are also necessary to prevent exposure to lead.
Respirators:
When respirators are used to supplement engineering and work practice controls to comply with the PEL and all other requirements have been met, employee exposure, for the purpose of determining compliance with the PEL, may be considered to be at the level provided by the protection factor of the respirator for those periods the respirator is worn. Those periods may be averaged with exposure levels during periods when respirators are not worn to determine the employee’s daily TWA exposure. The respiratory protection program will be conducted in accordance with 29 CFR 1910.134 (b) through (d) (except (d)(1)(iii)), and (f) through (m). The company will provide a powered air-purifying respirator when an employee chooses to use this type of respirator and such a respirator provides adequate protection to the employee.
Respirators must be used during: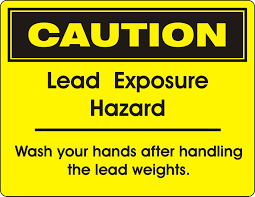
- Periods necessary to install or implement engineering or work-practice controls.
- Work operations for which engineering and work-practice controls are not sufficient to reduce employee exposures to or below the permissible exposure limit.
- Periods when an employee requests a respirator
Protective Clothing & Equipment:
If an employee is exposed to lead above the PEL, without regard to the use of respirators or where the possibility of skin or eye irritation exists, the company will provide at no cost to the employee appropriate protective work clothing and equipment such as, but not limited to:
- Coveralls or similar full-body work clothing;
- Gloves, hats, and shoes or disposable shoe coverlets; and
- Face shields, vented goggles, or other appropriate protective equipment.
Housekeeping:
- All surfaces shall be maintained as free as practicable of accumulations of lead.
- Floors and other surfaces where lead accumulates may not be cleaned by the use of compressed air.
- Shoveling, dry or wet sweeping, and brushing may be used only where vacuuming or other equally effective methods have been tried and found not to be effective.
- Where vacuuming methods are used, the vacuums shall be used and emptied in a manner which minimizes the reentry of lead into the workplace.
Hygiene Facilities & Practices:
The following is requirements pertain to all areas where employees are exposed to lead above the PEL, without regard to the use of respirators:
- No storage or consumption of food or beverages.
- No tobacco product storage or use.
- No cosmetics stored or used.
- No personal clothing or articles, except in authorized change areas
Change rooms:
Clean change rooms are provided for employees who work in areas where their airborne exposure to lead is above the PEL. Change rooms are equipped with separate storage facilities for protective work clothing and equipment and for street clothes which prevent cross-contamination. Employees who are required to shower after work shifts are not allowed to leave the workplace wearing any clothing or equipment worn during the work shift.
Showers:
Employees who work in areas where their airborne exposure to lead is above the PEL must shower at the end of the each work shift.
Signs:
Proper signs will be posted at the entrance and exits to all lead hazard areas, No other signs or statements may appear on or near any lead hazard sign which contradicts or detracts from the meaning of the required sign. All lead hazard signs will be kept illuminated and cleaned as necessary so that the legend is readily visible. The signs will contain the following or other appropriate wording/warning:
WARNING
LEAD WORK AREA
POISON
NO SMOKING OR EATING
Employee training will consist of: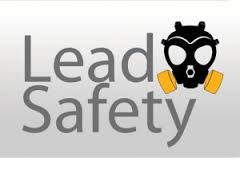
• specific OSHA requirements contained in ◦ 1910.1025 – OSHA Lead Standard ◦ 1910.1025 App A – Substance data sheet for occupational exposure to lead ◦ 1910.1025 App B – Employee standard summary.
• specific nature of the operations which could result in exposure to lead above the action level.
• purpose, proper selection, fitting, use, and limitations of respirators;
• purpose and a description of the medical surveillance program, and the medical removal protection program including information concerning the adverse health effects associated with excessive exposure to lead (with particular attention to the adverse reproductive effects on both males and females);
• engineering controls and work practices associated with the employee’s job assignment;
• contents of the company compliance plan.
• instructions that cheating agents should not routinely be used to remove lead from their bodies and should not be used at all except under the direction of a licensed physician.
• materials pertaining to the Occupational Safety and Health Act A copy of the OSHA standard 1910.1025 and its appendices will be readily available to all affected employees.
Click the below link to know more details about Lead in different field and guidelines