Types of Control:
At the source of the hazard
a. Elimination – Getting rid of a hazardous job, tool, process, machine or substance is perhaps the best way of protecting workers. For example, a salvage firm might decide to stop buying and cutting up scrapped bulk fuel tanks due to explosion hazards.
b.Substitution – Sometimes doing the same work in a less hazardous way is possible.For example, a hazardous chemical can be replaced with a less hazardous one.Controls must protect workers from any new hazards that are created.
Engineering control:
a. Redesign – Jobs and processes can be reworked to make them safer. For example,containers can be made easier to hold and lift.
b. Isolation – If a hazard cannot be eliminated or replaced, it can some times be isolated, contained or otherwise kept away from workers. For example, an insulated and air-conditioned control room can protect operators from a toxic chemical.
c. Automation – Dangerous processes can be automated or mechanized. For example, computer- controlled robots can handle spot welding operations in car plants. Care must be taken to protect workers from robotic hazards.
d. Barriers – A hazard can be blocked before it reaches workers. For example, special curtains can prevent eye injuries from welding arc radiation. Proper equipment guarding will protect workers from con tacting moving parts.
e. Absorption – Baffles can block or absorb noise. Lockout systems can isolate energy sources during repair and maintenance. Usually, the further a control keeps a hazard away from workers, the more effective it is.
f. Dilution – Some hazards can be diluted or dissipated. For example,ventilation systems can dilute toxic gasses before they reach operators.
Administrative controls:
a. Safe work procedures – Workers can be required to use standardized safety practices. The employer is expected to ensure that workers follow these practices. Work procedures must be periodically reviewed with workers and updated.
b. Supervision and training – Initial training on safe work procedures and refresher training should be offered. Appropriate supervision to assist workers in identifying possible hazards and evaluating work procedures.
c. Job rotations and other procedures can reduce the time that workers are exposed to a hazard. For example, workers can be rotated through jobs requiring repetitive tendon and muscle movements to prevent cumulative trauma injuries. Noisy processes can be scheduled when no one is in the workplace.
d. Housekeeping, repair and maintenance programs – Housekeeping includes cleaning, waste disposal and spill cleanup. Tools, equipment and machinery are less likely to cause injury if they are kept clean and well maintained.
e. Hygiene – Hygiene practices can reduce the risk of toxic materials being absorbed by workers or carried home to their families. Street clothing should be kept in separate lockers to avoid being contaminated by work clothing. Eating areas must be segregated from toxic hazards. Eating should be forbidden in toxic work areas. Where applicable, workers should be required to shower and change clothes at the end of the shift.
Personal protective equipment:
Personal protective equipment (PPE) and clothing is used when other controls measures are not feasible and where additional protection is needed. Workers must be trained to use and maintain equipment properly. The employer and workers must understand the limitations of the personal protective equipment. The employer is expected to require workers to use their equipment whenever it is needed. Care must be taken to ensure that equipment is working properly. Otherwise, PPE may endanger a workers health by providing an illusion of protection.
Monitoring controls:
The effectiveness of controls must be checked regularly. Evaluate and monitor hazard controls during inspections, routine maintenance, and other activities.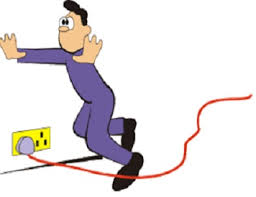
Ask the following questions –
a. have the controls solved the problem?
b. is any risk to workers posed by the controls contained?
c. are all new hazards being identified?
d. are significant, new hazards appropriately controlled?
e. are accident reports being analyzed?
f. are any other measures required?
Document control activities to track their effectiveness, if necessary re-evaluate hazards and implement new control measures.
Safe work procedures:
Through the completion of a Job Hazard Analysis, sometimes hazards are identified and cannot be eliminated or engineered out of a particular task. Safe Work Procedures are step by step instructions that allow workers to conduct their work safety when hazards are present. A Safe Work Procedure identifies the materials and equipment needed, and how and when to use them safety.
Safe Work Procedures are generally prepared for –
a. critical high risk jobs where accidents have or could result in severe injuries;
b. hazardous work where accidents occur frequently;
c. new or altered tasks have been introduced;
d. new equipment has been added to a process;
e. a job that requires many detailed tasks;
f. where two or more workers required for a job, and each must perform specific tasks simultaneously; and
g. specific tasks are done infrequently.
Safe Work Procedures must include:
a. regulatory requirements;
b. necessary personal protective equipment;
c. required training;
d. worker responsibilities;
e. specific sequence of steps to follow to complete the work safely;
f. required permits; and
g. emergency procedures.
An example of a task that requires the development of a safe work procedure is confined space entry. Individuals who must work within confined spaces must ensure that safe work procedures are developed and followed to maximize life safety.
Personal protective equipment (PPE):
Personal protective equipment means any equipment which is intended to be worn or held by a person at work and which protects him against one or more risks to his health or safety and any additional accessory designed to meet that objective;
PPE is usually chosen to provide protection appropriate to each of type of hazard present. There are specifications for the types of PPE used for protecting an individual’s head, eyes, footwear, limb and body, fire retardant clothing, respiratory, hearing, and personal flotation devices.
It may also include required apparel for example when traffic hazards are present high visible and distinguishable “vests must be worn”
Documenting HIRA:
Responsibility and accountability
Proper management of hazards sporadically identified in the workplace can be done through effective process. Ultimately, the individual or team who identified the hazard must ensure proper
communication of the hazard to the appropriate workplace authority (manager, department head, or designated person). Each HIRA must be fully documented. The HIRA form must be completed by the HIRA team and signed by the in charge personnel of the area. Departments responsible for the hazards and their control are required to maintain all records of assessments for at least 3 years. (In some cases, legislative requirements will determine the minimum time to retain records).
The appropriate authority is responsible for ensuring that effective and timely controls are applied to the hazard and communicating the results back to the originator. Management or employer must endorse and approve the HIRA results. Employer must communicate all HIRA to employees, monitor the follow up action and keep the records. The HIRA Form (Link below the page) is an example to document the HIRA process.
Documenting process:
Instructions to team leader and persons conducting HIRA :
- complete HIRARC Form. It is recommended to use a single form for each work process;
- record the names and designation of HIRAC team members;
- outline the process workflow and indicate in the form under ‘process/ location column;
- list all activities ( routine and non-routine) for each work process under the “Work Activity” column;
- identify the hazards associated with each activity and record in “Hazard” column;
- determine the effect of each hazard identified and record in “Effect” column;
- record any existing hazard control measures;
- determine likelihood (L) from Table A and severity (S) from Table B for eachhazard. Assign P and C rating in respectively column. The existing control measures should be take into consideration while determine (L) and (S);
- by using Risk Matrix ( Table C and D ) assign one risk and record in “Risk” column;
- based on the risk assigned, recommend appropriate risk control measures ( see Table D);
- assign a suitable person to implement the recommended risk control and indicate the follow up action date and status;
- repeat the HIRA for other activities and process;
- conduct another round of HIRA after control measures have been implemented; and
- review HIRA for every three years or whenever there are changes in process or